How does DFT differ from the other steel making processes?
Steel is an integral part of the construction industry and is the most widely used and most recycled material. Steel is available in various forms – from stainless and high-temperature steel to flat carbon products. Steel is one of the most innovative materials in the world. The steel industry’s step to achieve 100% efficiency has led to constructive discussions and advancement in technology. DFT is the latest technology in the steel industry which helps in manufacturing universal hollow steel pipes. It allows the buyers to customize their steel pipe according to the design. APL Apollo was the one to introduce DFT in India. Let us look at some of the other processes to understand the importance and necessity of DFT.
MIDREX:
It is a steel making and iron making process that helps in the production of Direct Reduced Iron. It is a gas-based shaft furnace process that helps in solid-state reduction process which reduces iron ore pellets in Direct Reduced Iron (DRI). The capacity of production has increased to 1.8 million tons per year in 2007.
The MIDREX process is effective because of
Continual refinement of the process which includes increases heat recovery,
Larger capacity shaft furnaces and
Hot briquetting.
Electric Arc Furnace:
An Electric Arc Furnace is an extremely hot enclosed space in which heat is produced by means of electrical arcing. The electric arc is produced between the electrodes. This process is used for melting the metals. It is used to produce mini steel structural bars and steel rods. There are two types of Electrical Arc Furnaces – they are alternating current (AC) and direct current (DC) operated the electric furnace.
COREX:
It is a smelting reduction process which combines a melter gasifier with a reduction shaft. The main inputs for this process are lump iron ore, non-coking coal, and oxygen. It helps in cost-efficient and environment-friendly COREX, production of hot metal. It is accepted as a commercially proven technology by fulfilling more stringent ecological regulations, utilization of low cost, highly available low-grade raw material.
Direct Forming Technology:
This technology has brought a revolutionary change in the steel pipe production industry. This helps in producing universal hollow shapes of pipe to fit customer requirements. It is an innovative route to pipe production. Compared to other traditional steelmaking processes it is completely automatic and computerized. Set-up operation of DFT is accurate and fast as compared to others. It enables buyers to get pipes according to the size they want, without compromising on the quality. This method gives an undisputed advantage in terms of production capability, cost reduction and flexibility. These square and rectangular hollow sections are lesser in weight and superior in strength as compared to other methods of steel tube manufacturing. DFT gives an advantage of on-time delivery of high-quality material.
Thus, switching to DFT has proven to be sustainable and cost-efficient that will ultimately fuel the growth of the industry.
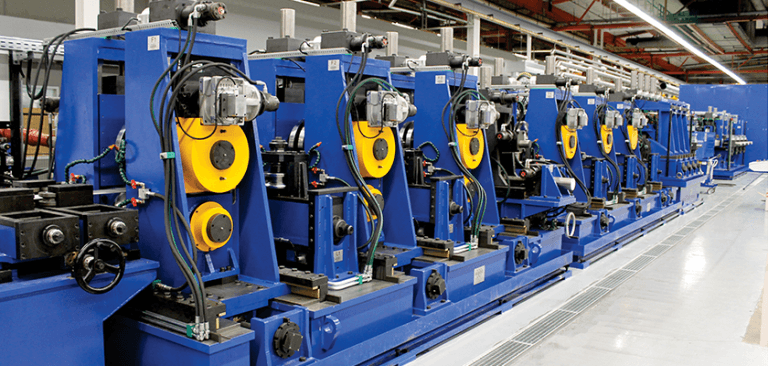